A Complete Guide to Picking the Best Chemical Defoamer for Your Needs
A Complete Guide to Picking the Best Chemical Defoamer for Your Needs
Blog Article
Comprehending Just How a Chemical Defoamer Functions to Boost Industrial Processes
Chemical defoamers play an essential function in optimizing industrial procedures by properly alleviating foam-related obstacles. What remains to be discovered is how these defoamers can be tailored to meet specific functional needs.
What Is a Chemical Defoamer?
A chemical defoamer is a compound particularly formulated to reduce or remove the development of foam in different industrial procedures. Frothing can hinder production performance, influencing the high quality and performance of items in industries such as food and drink, drugs, and wastewater therapy. Defoamers are vital in these applications, as extreme foam can lead to functional difficulties, such as overflow, reduced blending efficiency, and prevented warmth transfer.
These representatives normally include a mix of surfactants, oils, and various other additives that function to destabilize the foam framework. They are developed to promptly migrate to the foam's surface area, successfully breaking the surface area tension and enabling for the collapse of bubbles. The selection of an ideal defoamer is vital, as various formulas might be tailored for details processes or sorts of foam (Chemical Defoamer). Elements such as compatibility with other components, temperature level stability, and the desired application play a significant duty in the effectiveness of a defoamer.
Systems of Defoaming Activity
The mechanisms of defoaming action include intricate interactions between the foam and the defoamer framework. At the core of this process is the reduction of surface area stress at the user interface of the liquid and gas phases. When a defoamer is introduced to a lathering system, it moves rapidly to the surface area of the foam bubbles, displacing the maintaining representatives that add to foam stability. This displacement deteriorates the foam framework, leading to bubble coalescence.
As smaller sized bubbles merge into larger ones, the overall security of the foam diminishes. Furthermore, certain defoamers may include hydrophobic components that enhance their capability to undercut the foam by producing a barrier that prevents bubble development. This twin action-- surface area stress decrease and destabilization-- enables an extra effective malfunction of foam.
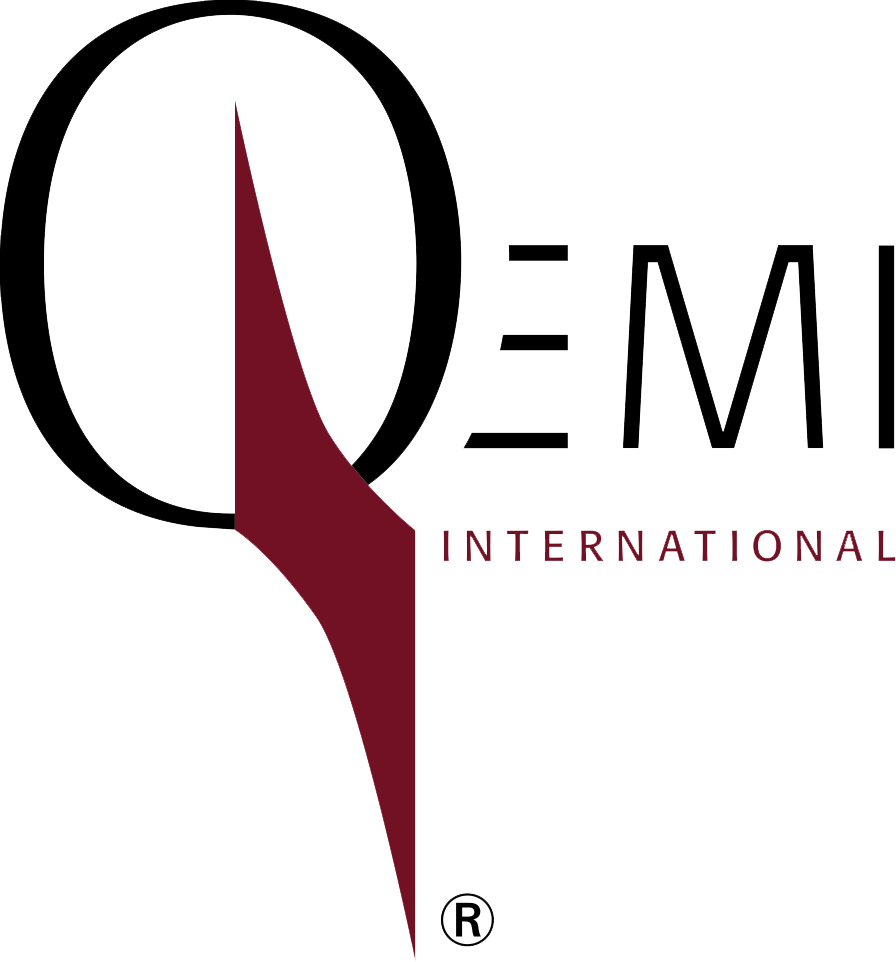
Additionally, the thickness and dispersing qualities of the defoamer play essential duties in its efficiency. A well-formulated defoamer will certainly guarantee fast movement and optimal efficiency, lessening foam development throughout commercial procedures. By understanding these systems, markets can better choose and use chemical defoamers to enhance operational performance and item top quality.
Sorts Of Chemical Defoamers
Chemical defoamers can be classified right into numerous kinds, each tailored to specific applications and foam challenges. The key classifications consist of silicone-based, non-silicone-based, and powder defoamers.
Silicone-based defoamers are very reliable as a result of their ability to spread quickly across liquid surface areas. They offer superb foam reductions and stability, making them suitable for numerous industrial applications, consisting of layers and adhesives. Non-silicone-based defoamers, on the other hand, commonly rely upon organic substances like fatty acids or esters. These are especially favored in food and drink markets because of their reduced poisoning and governing conformity.
Powder defoamers are composed of strong particles that can be contributed to completely dry processes or formulations. They are often utilized in processes where fluid defoamers may not work, giving an one-of-a-kind service for details applications, such as in the manufacturing of specific kinds of powders or plastics.
Furthermore, each kind of defoamer can be tailored with various ingredients to enhance efficiency, such as emulsifiers or surfactants, enabling adaptability in dealing with various foaming circumstances throughout numerous industries.
Applications in Industrial Processes
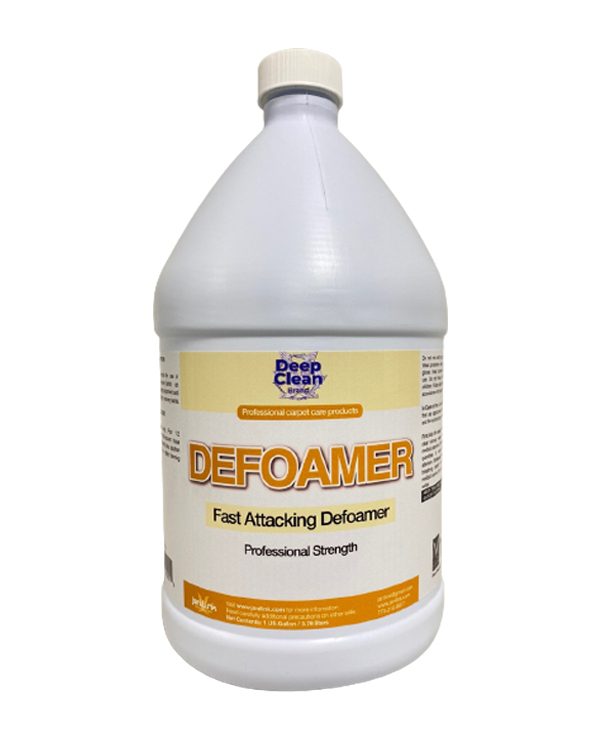
In the click to investigate food and drink industry, defoamers are critical throughout the production of juices, beers, and dairy items, where excessive foam can impede blending and filtering processes. By lowering foam development, defoamers assist maintain constant item top quality and maximize handling times.
In pharmaceuticals, the presence of foam throughout the mixing and solution of medicines can influence dosage precision and product security. Defoamers guarantee smooth procedures, thus facilitating the manufacturing of top notch pharmaceuticals.
Wastewater therapy facilities likewise depend this contact form on defoamers to manage foaming in aeration containers, which can otherwise lower treatment effectiveness and make complex sludge handling. By efficiently taking care of foam, these chemicals improve the total efficiency of therapy procedures and add to regulatory conformity.

Benefits of Utilizing Defoamers
While foam can provide substantial challenges throughout numerous industries, using defoamers provides various benefits that boost functional effectiveness and product integrity. Defoamers effectively remove or minimize foam formation, resulting in smoother production procedures and enhanced product top quality. This decrease in foam lessens interruptions during production, permitting continuous procedure and boosted throughput.
Furthermore, the application of more tips here defoamers can lead to set you back financial savings by decreasing the demand for excess resources and energy intake connected with foam monitoring. By maximizing the manufacturing process, manufacturers can attain higher returns and reduced waste, ultimately boosting success.
Additionally, defoamers add to better tools performance. Foam build-up can result in clogging, overflow, and devices wear, resulting in expensive downtime and upkeep. By stopping these issues, defoamers prolong the lifespan of equipment and minimize functional expenses.
Conclusion

A chemical defoamer is a substance especially developed to reduce or remove the formation of foam in various commercial processes. When a defoamer is presented to a foaming system, it moves quickly to the surface of the foam bubbles, displacing the supporting representatives that contribute to foam security. A well-formulated defoamer will certainly make certain fast movement and optimal performance, reducing foam formation throughout industrial procedures. Defoamers properly reduce or remove foam development, leading to smoother manufacturing processes and boosted product quality.In final thought, chemical defoamers play a crucial duty in improving industrial processes by effectively reducing foam formation.
Report this page